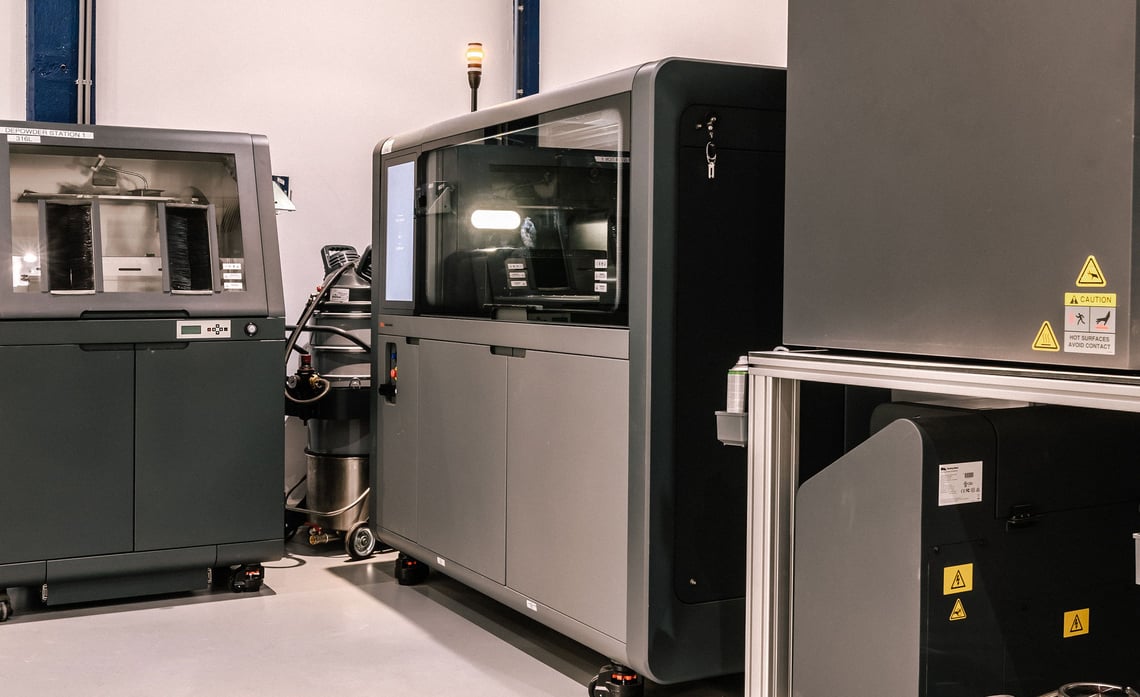
Wading through the technological lexicon of additive manufacturing can be challenging. This is amplified for potential users who may have never laid eyes on an industrial 3D printer like a Selective Laser Sintering machine or accompanying material powder like Nylon 12 [Versatile Plastic]. Shapeways makes it easier to navigate the sea of sometimes arduous terms and corresponding acronyms too, allowing users on all levels to gain a deeper understanding of the technology and the terminology.
Glossary
3D modeling – In developing a 3D representation of an object, designers and engineers rely on sophisticated tools and software to visualize, modify, and construct complex structures to be 3D printed.
3D printing – A method of digital fabrication created in the mid-80s, 3D printing allows for complex geometries to be made from a computer file. Materials are deposited layer by layer onto the print bed, until the desired structure is complete.
Additive manufacturing – The opposite of subtractive manufacturing where products are made by carving a structure out of another material, additive manufacturing adds materials layer by layer to build a shape. Also commonly referred to as 3D printing, additive manufacturing as a term tends to be used for industrial settings.
ABS – Acrylonitrile Butadiene Styrene is named for the three monomers making up its composition. ABS is an opaque 3D printing thermoplastic known for strength, durability, and resistance to impact, chemicals, and heat.
ASTM International – This organization serves to provide testing and technical standards for a wide range of items, to include products and systems, materials, and far more.
Binder Jetting – Created in the mid-90’s, Binder Jetting is named for the agents used to bond granular particles together layer by layer. This technology relies on one or more nozzles to build dense parts which are sintered in a furnace and left to strengthen, or a separate post-processing step may be used for coating and strengthening the final part. Binder liquid serves as the ‘glue’ to build parts.
Bounding Box – Serving as an imaginary outline of a box, enclosing the smallest area occupied by a 3D model, bounding box dimensions demonstrate recommended scale.
Build Plate – Also referred to as the 3D print bed, this area is designated for creation of the 3D printed part as each layer is deposited. In many cases, the size of a 3D print may only be limited by the size of the 3D printer’s build plate.
CAD – Computer-Aided Design is behind the creation of digital designs. In relation to 3D printing, designers are able to create a CAD file, convert it to a 3D file, and optimize the model for 3D printing.
CAM – Computer-Aided Manufacturing relies on software and other computerized tools for production.
DfAM – Design for Additive Manufacturing is a method of designing for the process to maximize the product for efficiency, cost, and strength.
DED – Directed Energy Deposition technology uses a laser or electron beam to melt materials, relying on the use of a robotic arm or a nozzle moving in multiple directions to complete the desired structure. DED is usually associated with metal 3D printing, and often on a large scale.
DMLS – Created by EOS, Direct Metal Laser Sintering is a type of Laser Powder Bed fusion that uses lasers to melt metal powder to create structures out of materials like Stainless Steel and Cobalt Chrome.
Elastomer – Typically used to create rubbery materials, elastomers are made up of chainlike polymers which are able to return to their natural state easily after being stretched.
FDM/FFF – Fused Deposition Modeling and Fused Filament Fabrication both fall under the category of Material Ext. Thermoplastic materials are heated into a molten form in the printhead and then deposited layer by layer onto the print bed, building the desired structure.
IATF-16949:2016 – Developed by the International Standard for Automotive Quality Management Systems and the International Automotive Task Force (IATF), this certification focuses on improvement, defect prevention, safety, and much more. IATF-16949:2016 is the most widely used standard for quality management systems in the automotive industry.
ISO – The International Organization for Standardization develops standards and certifications meant to strengthen innovation and offer solutions for areas like quality management in technology.
ISO 9001 – Developed by The International Organization for Standardization, ISO 9001 focuses on strengthening standards for quality control and management.
ITAR – Developed by the International Traffic in Arms Regulations, ITAR compliance is critical to many manufacturing companies, especially those who specialize in Injection Molding. This compliance is specific to our Michigan facility, Linear AMS.
Laser Sintering – For this type of 3D printing technology, a high-powered laser sinters powdered material together, layer by layer, to create a solid structure.
Material Jetting – MJ technology uses small, multi-nozzle printheads to project resin droplets onto the printhead. Multiple materials can be mixed within one print job for impressive texture and color.
Multi Jet Fusion – MJF technology, released by HP in 2016, is a subcategory of powder-bed fusion, and a powerful form of 3D printing that uses an inkjet array to move back and forth, separately releasing fusing and detailing agents onto the powder material. Thermal heat melts the layers together, until the desired structure is complete.
Nylon 11 – Shapeways offers this material as Nylon 11 [PA11 (SLS)]. A biocompatible nylon material used with SLS 3D printing technology, Nylon 11 [PA11 (SLS)] is known for durability and flexibility.
Nylon 12 – Shapeways offers both Nylon 12 [Versatile Plastic] and MJF Plastic PA12. These 3D printing materials are very popular due to its flexibility for thinner structures, and great strength for thicker structural components.
PA – Polyamide is nylon, a material widely used in 3D printing due to its high tensile strength.
Polyjet – Similar to inkjet technology, Polyjet 3D printing falls under the category of Material Jetting. The 3D printing method ‘jets’ drops of photopolymer material onto the print bed, to be cured by UV light. Advantages of Polyjet include the ability to make detailed, photorealistic parts. Polyjet was originally introduced by Objet, now Stratasys.
Polypropylene – A 3D printing material that Shapeways offers for rapid prototyping as well as manufacturing functional, end-use parts, Polypropylene is paired with either Multi Jet Fusion or Selective Laser Sintering technology. This material is popular for manufacturing automotive parts like coolant reservoirs and custom production tools.
Powder Bed Fusion – This category encompasses 3D printing technology like Selective Laser Sintering, Laser Powder Bed Fusion, and Electron Beam Melting (EBM). While each method varies, they all rely on a coating of power spread across the build surface to be melted or sintered, one layer after the other.
Rapid prototyping – The rapid prototyping process accelerates product development, allowing for quick iterations of product designs to evaluate aesthetics, fit, and functionality before moving on to full-scale production.
Selective Laser Sintering (SLS) – A subcategory of powder-based fusion, SLS technology relies on powerful lasers to sinter a thin layer of nylon powder distributed onto the print bed. SLS reigns as one of the most powerful and effective methods of 3D printing.
Stereolithography (SLA) – Known as the oldest method of 3D printing, SLA is still one of the most respected methods of 3D printing, falling under the Vat Polymerization category. SLA 3D printing relies on light reactive resins that are cured by UV light to build structures layer by layer. Manufacturers count on SLA technology for strong, intricate prototypes and precise functional parts that can be printed on the small or large scale.
Selective Laser Melting (SLM) – Used for complex metal parts, SLM 3D printing falls under the Powder Bed Fusion category, and is another form of Laser Powder Bed Fusion, which uses metals. SLM relies on lasers to melt fine metallic powder particles for creating extremely precise parts. Manufacturers choose SLM 3D printing for creating complex prototypes and high-performance end parts.
Slicer – This software slices the 3D models into layers, providing instruction for the 3D printer on how to print the corresponding design. The data for the 3D model is converted into a tool path that the 3D printer follows as each layer is deposited.
STL – One of the most common formats for storing 3D designs, STL files are usually created with a CAD program during the modeling process. This is an older file type that does not contain units or texture.
Thermoplastic Polyurethane (TPU) – This rubber-like material is used for elastic end-use products, 3D printed with SLS 3D printing technology. TPU is popular due to its flexibility, durability, and suitability for interlocking features.
Vat Polymerization – Centered around technology like the first 3D printing method, Stereolithography (SLA), vat polymerization is an AM process featuring liquid photopolymers or resins which are cured by UV light.
Wax Casting – 3D printing wax molds for casting metal is not only an age-old technique, but a fascinating one too, allowing designers to create highly detailed parts for applications like fine jewelry.
Learning about 3D printing and all it has to offer can be exciting–not to mention the exhilaration of actually putting the technology to use for manufacturing innovative products previously impossible to make via traditional methods. That doesn’t mean that 3D printing or additive manufacturing is easy to navigate in terms of production; however, Shapeways is in the business of simplifying that for manufacturers of all sizes.
About Shapeways
Enjoy the benefits of this advanced technology and a wide range of materials from Shapeways for 3D printing your creations with accuracy, complex detail, and no minimum or limits in terms of mass customization or single part orders. Shapeways has worked with over 1 million customers in 160 countries to 3D print over 21 million parts! Read about case studies, find out more about Shapeways solutions, and get instant quotes here.